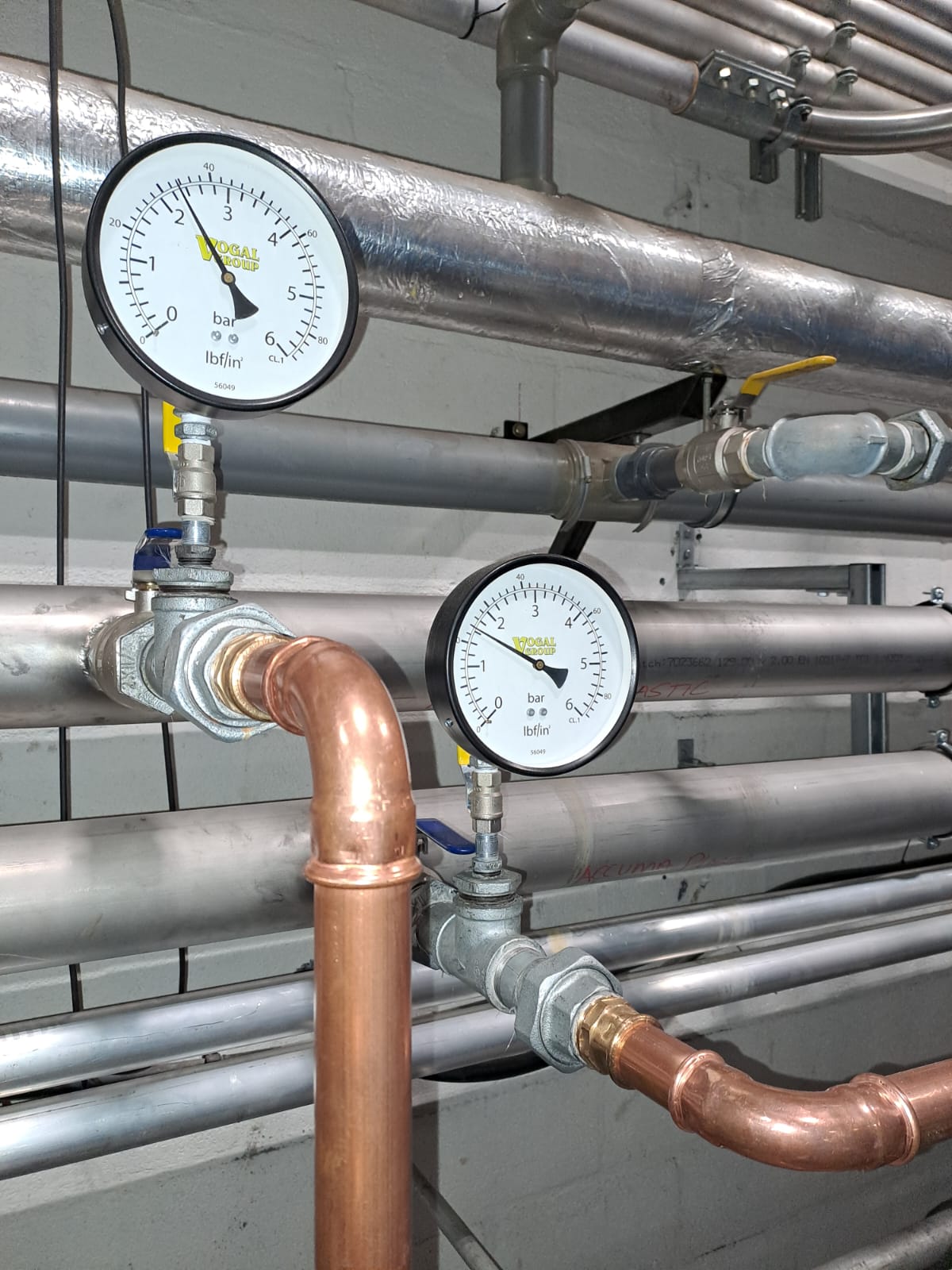
We completed an upgrade to a critical cooling system, while ensuring there was limited and controlled, disturbance to production. Our customer’s factory had an ageing, inefficient cooling system, that could not meet their immediate needs, and they had future plans for expansion. The system provides cooling to plastic extrusion moulding machines. The work needed to be done urgently, with summer fast approaching, and before high ambient air temperature adversely affected the efficiency of the legacy system. Furthermore, production downtime had to be kept to the absolute minimum. This was a 24/7 operation, and our customer wanted to keep it that way as the work was delivered.
Vogal Group engaged the services of a cooling system supplier and quickly established the cooling demand for each machine (existing and future) within the factory. This gave us the overall cooling system requirements, which in turn allowed us to scope a new cooler, pipework and pumps. Working with our preferred suppliers, our procurement team sourced an appropriate cooling water system and associated equipment including cooler, pumps, controls and 400 metres of stainless-steel pipework.
At the same time, we conducted a detailed survey of the factory, and our engineering design team produced a 3D model that enabled our pipework installation team to accurately establish pipe routes. This provided the detail required to manufacture the pipework off-site, in our workshop in Peterborough. The prefabricated pipework was transported to the site and installed, while the factory was still running. Final connections to the machines, coolers and pumps were co-ordinated with the production schedule and made at a time that resulted in minimal downtime.
Our smart approach minimised the disruption to our customer’s ongoing operations. Our in-house M&E turnkey project capability allowed us to deliver the complete ‘solution’ under one contract arrangement and benefited our customer as we did the background work, and they only had to deal with one Project Manager. Our Project Manager made it happen.
This project provided an upgraded cooling water system to not only meet the near-term demands but also future-proofed our customer’s factory for the planned future expansion. We completed the project both on-time and in-budget, with no negative impact on manufacturing production.
If you need external support with your pipework installations, please Contact us